In some equipped with standardized spot color matching system printing plant even color centers, often due to the purchase of some equipment is not up, the staff lack formal training, there are not enough resources to learn more about color functions standardized spot color matching system, etc. For various reasons, the manual color measurement method is still used to adjust the spot color, which is contrary to the original intention of the printing factory to standardize the color matching system. So, how can we make the standardization color matching system work best? This requires the printing company to have an in-depth understanding of the standardized color matching system.
Standardized color matching system
A complete set of standardized color matching system mainly includes the following aspects:
1 can directly modify the L*a*b* value and the color matching software and the supporting spectrodensitometer that effectively avoid the metamerism function;
2 multi-stage ink color display machine, and equipped with a fine ink meter that can finely adjust the ink volume to 0.005mL per grid;
3 electronic scales with a rated load not exceeding 250g, preferably imported products with a precision of up to 3 decimal places;
4 drying oven, used to simulate the normal drying temperature of the printing press;
5 multi-source small light boxes, including D50, D65, TL and UV light sources;
6 It is best to equip with an instrument that can test the performance of spot color inks such as abrasion resistance and light resistance.
How to build a complete ink database
To make a complete ink database, in addition to requiring the operator to have professional technical knowledge, a set of about 20 basic spot color inks with high concentration and covering the color gamut required by the ink market (hereinafter referred to as "base ink" is required. "), so that the special color matching system can use this set of base ink to match the spot color ink. The reason why the base ink concentration must be high is that if the concentration of the base ink is insufficient, it is necessary to open a large ink key and use more ink for printing, which not only causes the printed sheet to be printed, but also needs to be added if the printed sheet is quickly dried. The amount of powder sprayed, which in turn makes the color of the printed sheet dry and the color before drying is very different, and may also cause hidden troubles for post-press processing. Therefore, it is necessary to ensure that the base ink has a sufficient concentration to print the desired spot color.
In addition, the standard color difference between the base ink of each batch of incoming goods and the base ink in the ink database should be controlled within one, otherwise each time the spot color is allocated, it takes a long time to adjust and modify the information in the ink database.
Precautions for using a standardized tone color distribution system
(1) In order to prevent the large color difference of the spot color ink during printing, each time the spot color is allocated, the paper used in the batch printing must be used for the test printing, and it is necessary to understand the use of the formula through experiment. The spot color of the spot color ink is printed on the printing machine, and is used as a reference standard to predict the ink opening degree of the spot color ink during the official printing.
(2) When printing with spot color inks, it is necessary to test the color difference before and after the ink is dried in the ink-changing room to test the spot color inks on various papers, especially in the substrate with strong permeability (such as books). Color difference when printing on paper). If the color difference of the spot color ink before and after printing on the book paper can not be predicted in time, it will bring certain losses to the printing enterprise. Because the color difference of the book paper before and after drying is usually above 4, and the average customer receives the goods with a color difference of less than 2 before and after the print drying. It takes about 15 hours for the printed matter to be completely dry from printing to printing. If the color difference before and after the print is out of the standard range, it needs to be reprinted.
(3) For the customer's requirements for post-press processing (such as light, film, etc.), it is necessary to further test and simulate the color sample to meet the customer's requirements.
How to avoid buying a color matching system that does not meet the standard
The author found that most of the problems in the non-standard color tone distribution system appeared on the multi-segment color display machine for making color strips, especially the precision ink meter that can be finely adjusted to 0.005mL per grid. This is mainly because most of the multi-segment color machines currently on the market do not have excellent performance of the ink roller and components. In addition to being easily damaged, the printed color bars are not up to standard. There are also a number of multi-segment colorizers that allow the customer to adjust the pressure on their own, increasing the complexity of making color bars and shirking the responsibility for poor repeatability on the user.
In order to avoid the purchase of substandard color matching systems, the best method is to require the supplier to demonstrate the printing process of the color strips required by the user. For example, it can finish the printing of the color strips in about 30 minutes; it can print the spot color with the difference of less than 1 on the general coated paper and book paper; it can easily demonstrate the cold ash and the low concentration in the color code book. Warm gray spot color. It should be noted that the thickness of the ink layer of the exemplary spot color strip must be able to print smoothly on the press at one time.
The market price of a complete standardized color tone distribution system is about 250,000 yuan. Let's not mention the advantage of using a standardized color tone matching system to improve the quality of printed products. For example, the printers need to manually deploy 6 spot colors every day. For each spot color, it is no longer necessary to spend a lot of time on the machine. Adjustments and corrections save an average of 1 spot color ink for 20 minutes, and 6 spot colors save a total of 2 hours of production time. Calculated by the printing machine's production cost of 1000 yuan / hour, you can save 50,000 yuan in 25 working days per month, or you can spend an extra 50 hours of production time. I believe this will be a good investment.
The above content is reproduced in the "Printing Technology" official WeChat (Printech1957), authorized by the company to publish, copyright, piracy will be investigated!
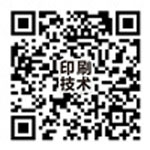
Study Room Desktop,Wooden Office Table ,Working Wooden Desk,Study Work Desk
Foshan Chengda Furniture Co.,ltd , https://www.catalogfur.com