Blister packs are those in which the drug is placed in a cavity (referred to as a "blister" or "bubble eye") in a plastic hard-formed plastic sheet, and then a sheet is gravure-printed and coated with a protective agent and adhesive. The aluminum foil of the agent is heat-sealed with the plastic hard film so that the medicine can be safely protected. The main materials for blister packs are pharmaceutical FFP aluminum foils, plastic hard sheets (PVC PVC) and adhesives.
Please pay attention to the history and status quo of adhesives for pharmaceutical blister packaging, and find out the direction of development in order to promote the survival of the fittest and the fittest of pharmaceutical packaging materials.
Blister packaging adhesives, early use of single-component pressure-sensitive adhesives. The main components of pressure-sensitive adhesives include synthetic resin adhesives (including natural rubber, synthetic rubbers, celluloses, polyacrylates), adhesives (including rosin, rosin esters, various petroleum resins, epoxy resins or phenolic resins, etc.) , Plasticizers (including chlorinated paraffins, phthalates), antioxidants, stabilizers, crosslinkers, colorants, and fillers. In the early days, pressure sensitive adhesives were based on natural rubber. The formula was 100 parts of plasticized natural rubber, polyterpene resin had a melting point of about 75°C, and petroleum resin contained 5 parts and partially polymerized. Methyl dichloroquinoline 2 parts mixed.
Another formula consists of 100 parts of smoked rubber tablets, 50 parts of zinc oxide, 75 parts of hydrogenated rosin, and a small amount of tackifier and plasticizer. Later, synthetic rubbers and synthetic resins were used instead of natural rubber. Among them, acrylates and their copolymers were most commonly used. For example, acrylic copolymer emulsions were used to make high-strength pressure-sensitive adhesives. The mixing ratio and manufacturing method was 100 parts of 43% solids. Amount of butyl acrylate-acrylic acid 2-ethylhexyl ester-vinyl acetate copolymer emulsion (composition ratio of 50:17:33) and 30 parts of 50% solid content of ethylene-vinyl acetate-vinyl chloride copolymer emulsion (composition The ratio was 19:36:45). The mixture was coated on a corona-discharged polypropylene film and dried at 110°C for 1 minute to form a pressure-sensitive adhesive tape. This tape is stripped of stainless steel. The strength is 600g/25mm. With the continuous improvement of the hygienic performance requirements of pharmaceutical packaging materials, due to the odor added to the adhesives of natural rubber ratio adhesives, and some toxic, it has not been used in pharmaceutical and food composite packaging, but acrylic pressure sensitive Glue still has certain advantages, such as because it is a single component, it will not cross-link curing, do not have to glue, simple to use; unfinished glue will not degenerate even if it is overnight or longer, as long as sealed airtight preservation It can be; then there is a good surface state of the adherend, many non-polar materials such as plastics, metal materials, small surface tension can also be firmly bonded. However, due to the wide variety of materials in the packaging of compound drugs, companies have turned to two-component polyurethane adhesives for the compounding of polar plastics and non-polar materials.
At present, pressure-sensitive adhesives for pharmaceutical flexible packaging composites have been replaced by polyurethane adhesives, mainly ester-soluble polyurethane adhesives. Such adhesives are two-component ester-soluble adhesives whose main agent is a polyether or polyester polyol modified aromatic isocyanate, a hydroxyl-containing polyurethane polyol, and a curing agent that is a combination of aromatic isocyanate and trimethylolpropane. These adhesives have excellent performance, mature technology, and many varieties, but they are toxic, costly, and emit large amounts of solvents that pollute the environment. For a long period of time, the composite material may undergo hydrolysis and release a carcinogenic substance, which seriously affects the operator's health. With the increasing awareness of environmental protection, the use of such adhesives continues to decline.
Application of Alcohol-soluble Polyurethane Adhesives: It is based on industrial alcohol as solvent, low production cost, good hygienic performance, harmless to humans, and no pollution to the environment. The disadvantage is that it is not resistant to high temperatures of 100°C and cannot be packaged with highly corrosive products. Another type of adhesive is an aqueous polyurethane adhesive based on water-soluble or water-dispersible solvents. Its advantage is that water replaces organic solvents. There is no danger of burning and the cost is low. However, poor adhesive properties.
At present, adhesives for composite flexible packaging materials are developing in the direction of solvent-free adhesives, and solvent-free adhesives are basically composed of two-component polyurethane adhesives. Their main agents and curing agents have high viscosity at room temperature and have fluidity. The curing agent is mixed according to the proportion. After the temperature is raised, the roller is applied to the substrate. Since the organic solvent is not used, the cost is reduced. There is no environmental pollution caused by the volatilization of the organic solvent, and the huge drying, heating, blowing, and exhaust emission devices of the device are omitted. , Reduced energy consumption. The product has no residual solvent damage, the production speed is increased, the maintenance cost is low, and the benefits are significant. In the field of pharmaceutical flexible packaging, it is the future development direction.
Author: Yuan may
Source: Packaging News
One of the Corten Steel Bbq Grill is that the surface doesn't need to be touched up with paint...ever! Each product details its own uniqueness, with color highlights and variations that are not only esthetically pleasing but also resistant to rust. In fact, corten steel BBQ grill has a weather resistance that is 4 to 8 times greater than ordinary steel!The surface of each of our special corten steel BBQ grill is aged to look as though the product has been in the elements for about a month.
Name | Steel Charcoal Burner bbq |
Material | Corten steel |
Cooking plate Size | Diameter 1000mm |
Base Size | 500*500*700mm |
Thickness | Base:2mm, Cooking plate:10mm |
Weight | 120KG |
Packing | Pallet/carton/wooden box packing |
Packing
Packing will by pallet/carton/ wooden box,according to different demand.
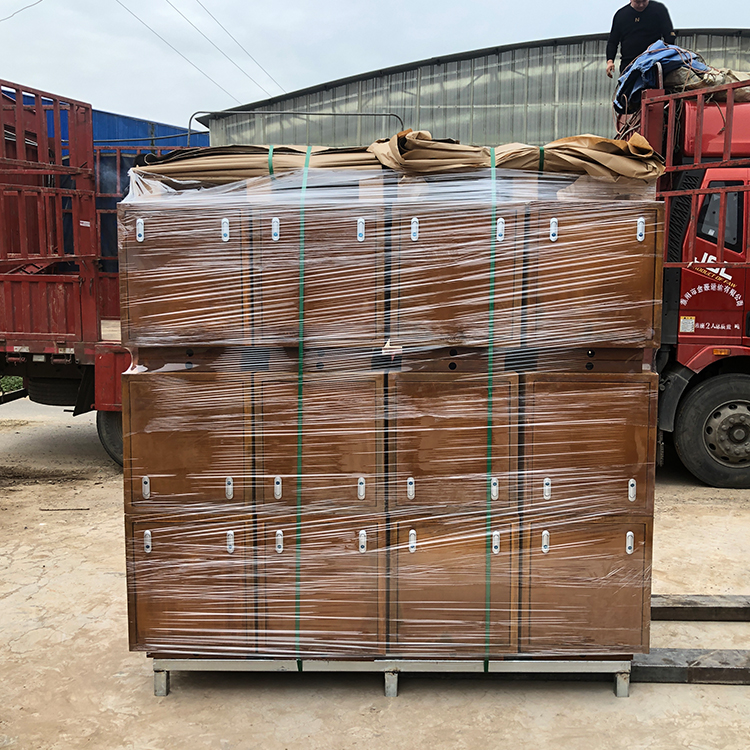
BBQ Grill,Smoker Grill,Barbecue Grill,Outdoor Grill
Henan Jinbailai Industrial Co.,Ltd , https://www.hnjblfirepit.com